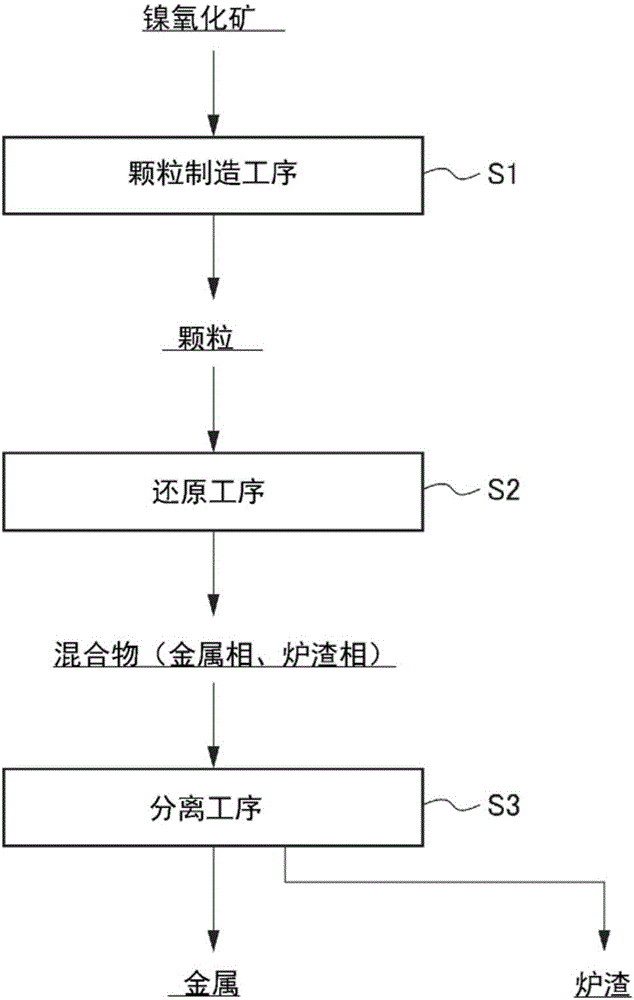
本發(fā)明涉及鎳氧化礦的冶煉方法、顆粒的裝入方法,更詳細地,涉及由作為原料礦石的鎳氧化礦形成顆粒,在冶煉爐中將所述顆粒還原加熱,從而進行冶煉的鎳氧化礦的冶煉方法以及將顆粒裝入所述冶煉爐的方法。
背景技術(shù):
:作為被稱為褐鐵礦或腐泥土的鎳氧化礦的冶煉方法,已知使用熔煉爐制造鎳锍的干式冶煉方法、使用回轉(zhuǎn)窯或移動爐床爐制造鎳鐵的干式冶煉方法、使用高壓釜制造混合硫化物的濕式冶煉方法等。將鎳氧化礦裝入冶煉工序時,進行用于將上述原料礦石顆粒化、漿料化等的前處理。具體而言,將鎳氧化礦顆?;?,即,制造顆粒時,與除上述鎳氧化礦以外的成分例如粘合劑、還原劑混合,進一步進行水分調(diào)節(jié)等后,裝入塊狀物制造機,例如,通常制成10~30mm左右的塊狀物(指顆粒、團塊等。以下,僅稱為“顆?!?。例如,為了實現(xiàn)保持通氣性、防止原料成分的不均勻等作用,即使將上述顆粒裝入冶煉爐,開始還原加熱等冶煉操作,維持其形狀也是重要的。例如,在專利文獻1中,公開了一種作為利用移動爐床爐制造鎳鐵時的前處理方法的技術(shù),所述技術(shù)在將含有氧化鎳和氧化鐵的原料與碳質(zhì)還原劑混合形成混合物的混合工序中調(diào)節(jié)混合物中的剩余碳含量,制造顆粒,將所述顆粒裝入爐內(nèi)進行還原工序。然而,碳質(zhì)還原劑與其他原料的“融合性”差,與不加碳質(zhì)還原劑的情況相比,制造的顆粒強度弱。將顆粒裝入冶煉爐時,在顆粒強度不足以至于由裝入時承受的力導致崩解的情況下,如上述專利文獻1(例如,參照段落[0061])所記載,存在必須采取添加粘合劑等用于得到所需強度的某些手段的問題?,F(xiàn)有技術(shù)文獻專利文獻專利文獻1:日本特開2004-156140號公報。技術(shù)實現(xiàn)要素:發(fā)明所要解決的問題本發(fā)明是基于上述實際情況而提出的,其目的在于,在通過由鎳氧化礦形成顆粒,在冶煉爐中將所述顆粒還原加熱,從而進行冶煉的方法中,提供能夠在維持顆粒強度的同時使冶煉工序(還原工序)中的冶煉反應有效地進行的鎳氧化礦的冶煉方法、將顆粒裝入所述冶煉爐的方法。解決問題的技術(shù)方案本發(fā)明人為了解決上述問題而進行了悉心研究。其結(jié)果是,發(fā)現(xiàn)了通過制造不含有碳質(zhì)還原劑的顆粒,將所述顆粒裝入冶煉爐,從而成為被碳質(zhì)還原劑覆蓋的狀態(tài),實施還原加熱處理,從而能夠在維持顆粒強度的同時使冶煉反應有效地進行,完成了本發(fā)明。即,本發(fā)明提供以下內(nèi)容。(1)本發(fā)明的第一發(fā)明是一種鎳氧化礦的冶煉方法,通過由鎳氧化礦形成顆粒,將所述顆粒還原加熱,從而進行冶煉,所述鎳氧化礦的冶煉方法的特征在于,具有:由所述鎳氧化礦制造顆粒的顆粒制造工序,以及,在冶煉爐中以規(guī)定的還原溫度將得到的顆粒還原加熱的還原工序;在所述顆粒制造工序中,不混合碳質(zhì)還原劑,而將含有所述鎳氧化礦的原料混合作為混合物,將該混合物塊狀化,形成顆粒,在所述還原工序中,將得到的顆粒裝入所述冶煉爐時,預先在該冶煉爐的爐床上鋪滿碳質(zhì)還原劑,將所述顆粒載置在該碳質(zhì)還原劑上,進一步在所述顆粒被碳質(zhì)還原劑覆蓋的狀態(tài)下對所述顆粒進行還原加熱。(2)另外,本發(fā)明的第二發(fā)明是如上述第一發(fā)明所述的鎳氧化礦的冶煉方法,其特征在于,在所述還原工序中,用碳質(zhì)還原劑進一步覆蓋載置在所述碳質(zhì)還原劑上的顆粒時,使從被覆蓋的顆粒的上端至所述碳質(zhì)還原劑層的表面為止的厚度為所述顆粒的高度方向大小的至少5%以上。(3)另外,本發(fā)明的第三發(fā)明是如上述第一或第二發(fā)明所述的鎳氧化礦的冶煉方法,其特征在于,將所述顆粒裝入所述冶煉爐時的溫度設定為600℃以下。(4)本發(fā)明的第四發(fā)明是一種顆粒的裝入方法,其是用于通過由鎳氧化礦形成顆粒,在冶煉爐中將該顆粒還原加熱,從而進行冶煉的顆粒的裝入方法,所述顆粒的裝入方法的特征在于,具有:由所述鎳氧化礦制造顆粒的顆粒制造工序,以及,將得到的顆粒裝入用于還原加熱的冶煉爐的顆粒裝入工序;在所述顆粒制造工序中,不混合碳質(zhì)還原劑,而將含有所述鎳氧化礦的原料混合作為混合物,將該混合物塊狀化,形成顆粒,在所述顆粒裝入工序中,預先在所述冶煉爐的爐床上鋪滿碳質(zhì)還原劑,將該顆粒載置在該碳質(zhì)還原劑上,用碳質(zhì)還原劑進一步覆蓋該顆粒使其處于被覆蓋的狀態(tài)。發(fā)明效果根據(jù)本發(fā)明,能夠在維持顆粒強度的同時使將顆粒還原加熱的還原工序中的冶煉反應有效地進行。附圖說明圖1是表示鎳氧化礦的冶煉方法的流程的工序圖。圖2是表示在鎳氧化礦的冶煉方法中的顆粒制造工序中的處理的流程的處理流程圖。圖3是示意性地表示將顆粒裝入冶煉爐內(nèi)的狀態(tài)的圖。具體實施方式下面,參照附圖詳細地說明本發(fā)明的具體實施方式(以下,稱為“本實施方式”)。需要說明的是,本發(fā)明并不限定于以下實施方式,在不改變本發(fā)明要旨的范圍內(nèi)可進行各種改變?!?.鎳氧化礦的冶煉方法》首先,對作為原料礦石的鎳氧化礦的冶煉方法進行說明。下面,舉例說明冶煉方法,所述冶煉方法通過將作為原料礦石的鎳氧化礦顆?;?,對該顆粒進行還原處理,從而生成金屬(鐵-鎳合金(以下,也將鐵-鎳合金稱為“鎳鐵”))和爐渣,分離該金屬和爐渣,從而制造鎳鐵。本實施方式的鎳氧化礦的冶煉方法是通過使用鎳氧化礦顆粒,將所述顆粒裝入冶煉爐(還原爐)中,進行還原加熱,從而進行冶煉的方法。具體而言,如圖1的工序圖所示,上述鎳氧化礦的冶煉方法具備:由鎳氧化礦制造顆粒的顆粒制造工序S1;在還原爐中以規(guī)定的還原溫度將得到的顆粒還原加熱的還原工序S2;以及,分離在還原工序S2中生成的金屬和爐渣,回收金屬的分離工序S3。<1-1.顆粒制造工序>在顆粒制造工序S1中,由作為原料礦石的鎳氧化礦制造顆粒。圖2是表示在顆粒制造工序S1中的處理的流程的處理流程圖。如圖2所示,顆粒制造工序S1具備:混合含有鎳氧化礦的原料的混合處理工序S11;將得到的混合物形成為塊狀物(造粒)的塊狀化處理工序S12;以及,干燥得到的塊狀物的干燥處理工序S13。(1)混合處理工序混合處理工序S11是混合含有鎳氧化礦的原料粉末,得到混合物的工序。具體而言,在所述混合處理工序S11中,混合作為原料礦石的鎳氧化礦以及鐵礦石、助熔劑成分、粘合劑等粒徑為例如0.2mm~0.8mm左右的原料粉末,得到混合物。在此,在本實施方式中,制造顆粒時,不混合碳質(zhì)還原劑而得到混合物,由不包含上述碳質(zhì)還原劑的混合物形成顆粒。如此地,作為原料粉末,不混合碳質(zhì)還原劑而制造顆粒,從而能夠抑制得到的顆粒的強度的降低。作為鎳氧化礦,無特別限定,可以使用褐鐵礦、腐泥土礦等。作為鐵礦石,無特別限定,例如,可以使用鐵品位為50%左右以上的鐵礦石、通過鎳氧化礦的濕式冶煉得到的赤鐵礦等。另外,作為粘合劑,例如,可舉例膨潤土、多糖類、樹脂、水玻璃、脫水泥餅等。另外,作為助熔劑成分,例如,可舉例氧化鈣、氫氧化鈣、碳酸鈣、二氧化硅等。在下述表1中示出原料粉末的部分組成(重量%)的一個實例。需要說明的是,作為原料粉末的組成,并不限定于此。[表1]原料粉末[重量%]NiFe2O3C鎳氧化礦1~250~60-鐵礦石-80~95-(2)塊狀化處理工序塊狀化處理工序S12是將混合處理工序S11中得到的原料粉末混合物形成為塊狀物(造粒)的工序。具體而言,在混合處理工序S11中得到的混合物中添加塊狀化所需的水分,例如,使用塊狀物制造裝置(滾動造粒機、壓縮成型機、擠出成型機等)等或通過人手形成顆粒狀的塊。作為顆粒的形狀,無特別限定,例如,可以為球狀。另外,作為形成顆粒狀的塊狀物的大小,無特別限定,例如,通過后述的干燥處理、預熱處理,使被裝入還原工序中的冶煉爐等的顆粒的大小(在球狀顆粒的情況下為直徑)為10mm~30mm左右。(3)干燥處理工序干燥處理工序S13是對在塊狀化處理工序S12中得到的塊狀物進行干燥處理的工序。通過塊狀化處理成為顆粒狀的塊的塊狀物含有過量例如50重量%左右的水分,成為發(fā)粘的狀態(tài)。為了使上述顆粒狀的塊狀物的處理變得容易,在干燥處理工序S13中,實施干燥處理,例如使塊狀物的固體成分為70質(zhì)量%左右,水分為30質(zhì)量%左右。更具體地,作為干燥處理工序S13中對塊狀物的干燥處理,無特別限定,例如,對塊狀物吹300℃~400℃的熱風,進行干燥。需要說明的是,該干燥處理時的塊狀物的溫度小于100℃。在下述表2中示出干燥處理后的顆粒狀的塊狀物中的固體成分組成(重量份)的一個實例。需要說明的是,作為干燥處理后塊狀物的組成,并不限定于此。表2在顆粒制造工序S1中,如上所述地混合含有作為原料礦石的鎳氧化礦的原料粉末,將得到的混合物造粒(塊狀化)成顆粒狀,使其干燥,從而制造顆粒。此時,在混合原料粉末時不混合碳質(zhì)還原劑,制造不包含碳質(zhì)還原劑的顆粒。得到的顆粒的大小為10mm~30mm左右,制造具有可維持形狀的強度的顆粒,例如,所述強度是,即使在從高度1m下落的情況下,崩解的顆粒的比例也為1%以下左右的強度。這種顆粒能夠承受裝入下一步的還原工序S2時的下落等沖擊,能夠維持該顆粒的形狀,而且,由于顆粒與顆粒之間形成適當?shù)目障?,所以使冶煉工序中的冶煉反應適當?shù)剡M行。另外,在該顆粒制造工序S1中,也可以設置預熱處理工序,所述預熱處理工序是在規(guī)定溫度下對上述在干燥處理工序S13中實施干燥處理的塊狀物的顆粒進行預熱處理的工序。如此地,對干燥處理后的塊狀物實施預熱處理,制造顆粒,即使在將還原工序S2中的顆粒在例如1400℃左右的高溫下還原加熱時,也能夠更有效地抑制由熱沖擊導致的顆粒破碎(破壞、崩解)。例如,能夠使裝入冶煉爐的全部顆粒中崩解的顆粒的比例為很小的比例,能夠更有效地維持顆粒的形狀。具體而言,在預熱處理中,在350℃~600℃的溫度下對干燥處理后的顆粒進行預熱處理。另外,優(yōu)選在400℃~550℃的溫度下進行預熱處理。如此地,通過在350℃~600℃、優(yōu)選400℃~550℃的溫度下預熱處理,能夠減少構(gòu)成顆粒的鎳氧化礦中含有的結(jié)晶水,即使在裝入約1400℃的冶煉爐,溫度急劇升高的情況下,也能夠抑制由該結(jié)晶水脫離導致的顆粒的崩解。另外,通過實施這種預熱處理,使構(gòu)成顆粒的鎳氧化礦、氧化鐵、粘合劑和助熔劑成分等粒子的熱膨脹分兩個階段緩慢地進行,由此,能夠抑制由粒子的膨脹差導致的顆粒的崩解。另外,作為預熱處理的處理時間,無特定限定,根據(jù)含有鎳氧化礦的塊狀物的大小適當?shù)卣{(diào)整即可,如果得到的顆粒是大小為10mm~30mm的通常大小的塊狀物,則能夠?qū)⑻幚頃r間設為10分鐘~60分鐘左右。<1-2.還原工序>在還原工序S2中,將顆粒制造工序S1中得到的顆粒在指定的還原溫度下還原加熱。通過在該還原工序S2中對顆粒進行還原加熱處理,從而進行冶煉反應,生成金屬和爐渣。具體而言,還原工序S2中的還原加熱處理是使用冶煉爐(還原爐)等進行的,通過將含有鎳氧化礦的顆粒裝入加熱至例如1400℃左右的溫度的冶煉爐中進行還原加熱。在本實施方式中,將上述得到的顆粒裝入冶煉爐時,預先在上述冶煉爐的爐床上鋪滿碳質(zhì)還原劑,將顆粒載置在上述鋪蓋的碳質(zhì)還原劑上。接著,用碳質(zhì)還原劑進一步覆蓋載置在碳質(zhì)還原劑上的顆粒使其處于被覆蓋的狀態(tài)。即,本實施方式的特征在于,將含有鎳氧化礦的顆粒還原加熱時,使顆粒處于被碳質(zhì)還原劑覆蓋的狀態(tài)。在下文進行更詳細地說明。在該還原工序S2的還原加熱處理中,首先,僅用例如一分鐘左右的時間在容易進行還原反應的顆粒表面附近將顆粒中的鎳氧化物和鐵氧化物還原,金屬化,成為鐵-鎳合金(鎳鐵),形成殼(shell)。另一方面,在殼中,隨著上述殼的形成,顆粒中的爐渣成分逐漸熔融,生成液相爐渣。由此,在一個顆粒中,分別生成鎳鐵金屬(以下,僅稱為“金屬”)和鎳鐵爐渣(以下,僅稱為“爐渣”)。然后,通過將還原工序S2中的還原加熱處理的處理時間進一步延長至10分鐘左右,從而使鋪蓋于冶煉爐的爐床的、為了進一步覆蓋顆粒而包圍的碳質(zhì)還原劑中不參與還原反應的剩余碳質(zhì)還原劑的碳成分進入鐵-鎳合金中,使熔點降低。其結(jié)果是,鐵-鎳合金溶解成為液相。如上所述,雖然顆粒中的爐渣熔融成為液相,但是,已經(jīng)分離生成的金屬和爐渣不會混雜在一起,通過隨后的冷卻,成為金屬固相與爐渣固作為單獨的相混合的混合物。與裝入的顆粒相比,所述混合物的體積收縮為50%~60%左右的體積。在上述冶煉反應最理想地進行的情況下,對于裝入的一個顆粒而言,得到一個金屬固相與一個爐渣固相混合的一個混合物,成為“不倒翁狀”形狀的固體。在此,“不倒翁狀”是指金屬固相與爐渣固相接合的形狀?;旌衔锞哂羞@種“不倒翁狀”的形狀時,由于上述混合物粒子的尺寸達到最大,因此,從冶煉爐回收時,回收的勞力和時間少,能夠抑制金屬回收率的降低。在本實施方式的鎳氧化礦的冶煉方法中,如上所述,在顆粒制造工序S1中,為了制造不包含碳質(zhì)還原劑的顆粒,將上述顆粒裝入在爐床上鋪滿碳質(zhì)還原劑的冶煉爐,用碳質(zhì)還原劑進一步包圍顆粒以進行覆蓋,在這種狀態(tài)下實施還原加熱處理。如此地,通過實施還原加熱處理,在維持顆粒強度,抑制還原加熱處理中的崩解的同時,能夠使冶煉反應有效地進行。<1-3.分離工序>在分離工序S3中,分離在還原工序S2中生成的金屬和爐渣,回收金屬。具體而言,從通過對顆粒進行還原加熱處理而得到的、包含金屬相(金屬固相)和爐渣相(包含碳質(zhì)還原劑的爐渣固相)的混合物中分離回收金屬相。作為從得到的金屬相和爐渣相的固體混合物中分離金屬相和爐渣相的方法,例如,不僅可以通過篩分除去不需要的物質(zhì),還可以利用比重分離、磁力分離等方法。另外,由于得到的金屬相和爐渣相潤濕性差,因此,能夠容易地分離,對于上述“不倒翁狀”的混合物而言,例如,通過實施設置規(guī)定的落差使所述混合物下落、或者通過在篩分時給予規(guī)定的振動等沖擊,能夠容易地從上述“不倒翁狀”的混合物中分離金屬相和爐渣相。如此地,通過分離金屬相和爐渣相,從而回收金屬相?!?.顆粒的裝入方法》然后,在上述鎳氧化礦的冶煉方法中,對用于由原料礦石的鎳氧化礦形成顆粒,在冶煉爐中將所述顆粒還原加熱,從而進行冶煉的將顆粒裝入冶煉爐的方法,進行更詳細的說明。本實施方式的特征在于,在上述顆粒制造工序S1中的混合處理工序S11中,不混合碳質(zhì)還原劑,例如,將作為原料礦石的鎳氧化礦與鐵礦石(氧化鐵)混合,成為混合物。接著,通過將得到的混合物塊狀化,制造不包含碳質(zhì)還原劑的顆粒。如此地,由于得到的顆粒的強度高于混合了碳質(zhì)還原劑的顆粒,因此,即使在下一步的還原工序S2中裝入冶煉爐時承受沖擊等的情況下,也能夠抑制上述顆粒的崩解。本實施方式的特征在于,如此地,制造不包含碳質(zhì)還原劑的顆粒后,將上述顆粒裝入用于還原加熱的冶煉爐時,如圖3(A)的示意圖所示,預先在冶煉爐1的爐床1a上鋪滿碳質(zhì)還原劑10,將制造的顆粒20載置在上述鋪蓋的碳質(zhì)還原劑10上。接著,如圖3(B)所示,對載置的顆粒20,進一步添加碳質(zhì)還原劑10,從而覆蓋包圍顆粒20,即,成為由碳質(zhì)還原劑20完全覆蓋顆粒20的狀態(tài)。在本實施方式中,在如此地成為由碳質(zhì)還原劑覆蓋圍繞顆粒周圍的狀態(tài)的基礎(chǔ)上,實施還原加熱處理。由此,在還原加熱時,由于圍繞顆粒周圍的碳質(zhì)還原劑不破壞顆粒的形狀,因此,上述碳質(zhì)還原劑發(fā)揮所謂殼的作用,使冶煉反應適當?shù)剡M行,有效地形成金屬與爐渣接合的“不倒翁狀”的塊狀物(包含金屬相和爐渣相的混合物)。通過冶煉反應得到的塊狀物是在由碳質(zhì)還原劑覆蓋的狀態(tài)下而得到的,上述塊狀物的尺寸為約6mm~18mm左右的大小,另一方面,例如,對于碳質(zhì)還原劑而言,例如,僅是次微米(Sub-Micron)粒子進行了微弱燒結(jié)。因此,將得到的塊狀物從冶煉爐中排出時,碳質(zhì)還原劑被粉碎,通過篩分等手段能夠容易地與塊狀物分離。另外,根據(jù)需要,通過使用振動篩等或利用比重差分級,能夠更有效地分離。在本實施方式中,在進行還原加熱處理的還原工序S2中,重要的是,圍繞裝入冶煉爐的顆粒周圍的碳質(zhì)還原劑不破壞顆粒的形狀。在還原工序中的冶煉反應中,在上述還原加熱初期形成的殼在確保還原環(huán)境中發(fā)揮了重要的作用,如上所述,在本實施方式中,覆蓋顆粒的碳質(zhì)還原劑所形成的空間(以下,僅稱為“空間”)發(fā)揮了上述殼的作用,維持了還原環(huán)境。由此,不需要像現(xiàn)有技術(shù)那樣使顆粒中含有碳質(zhì)還原劑,基于所含有的碳質(zhì)還原劑而形成殼,可以抑制顆粒強度的降低。另外,包圍顆粒的碳質(zhì)還原劑發(fā)揮了殼的作用,使冶煉反應有效地進行,因此,適當?shù)匦纬伞安坏刮虪睢钡膲K狀物。在此,作為碳質(zhì)還原劑,無特別限定,例如,可舉例煤粉、焦粉等。另外,作為碳質(zhì)還原劑的粒度,無特別限定,優(yōu)選能夠有效地覆蓋顆粒的大小。另外,進一步加入碳質(zhì)還原劑覆蓋在鋪蓋于爐床的碳質(zhì)還原劑上載置的顆粒時,無特別限定,例如,如圖3(B)的示意圖所示,從被覆蓋的顆粒20的上端至碳質(zhì)還原劑10層的表面為止的厚度“X”優(yōu)選為上述顆粒的高度方向(圖3(B)中的箭頭H)大小(在球狀顆粒的情況下為直徑)的至少5%以上。例如,考慮到顆粒尺寸通常為10~30mm左右的大小,則顆粒大小的5%為0.5mm~1.5mm左右。如此地,通過使圖3(B)所示的厚度X為顆粒20的高度方向H的大小的5%以上,從而能夠在可操作管理的范圍內(nèi),并且成為用碳質(zhì)還原劑完全覆蓋顆粒的狀態(tài),上述碳質(zhì)還原劑不破壞形狀,隨著冶煉反應的進行,更有效地發(fā)揮作為所謂的殼的作用。當厚度X小于顆粒尺寸的5%時,操作控制變得困難,由于操作上的偏差導致顆粒表面從碳質(zhì)還原劑層露出至冶煉爐內(nèi)的空間。在這種情況下,不能維持對于冶煉反應而言重要的殼內(nèi)(空間內(nèi))還原環(huán)境,不能進行適當?shù)囊睙挿磻?。另一方面,若厚度X為顆粒尺寸的5%以上,雖然能夠發(fā)揮上述效果,但是,即使厚度X過大,效果也不累積,使用的碳質(zhì)還原劑的成本增加。另外,當厚度X過大時,由于顆粒中的熱的傳導變得困難,燃料成本增加。因此,作為上限值,厚度X優(yōu)選為顆粒尺寸的10%以下左右。另外,作為將制造的顆粒裝入冶煉爐內(nèi)時的溫度,即,作為從開始將顆粒裝入冶煉爐內(nèi)至用碳質(zhì)還原劑完全覆蓋顆粒為止的操作時的溫度,優(yōu)選為600℃以下。另外,從使碳質(zhì)還原劑緩慢燒結(jié)的影響為最低限度的觀點出發(fā),更優(yōu)選為550℃以下。裝入顆粒時的溫度大于600℃時,覆蓋顆粒的碳質(zhì)還原劑可能開始燃燒。另一方面,在進行連續(xù)的冶煉處理的過程時,如果過于降低溫度,則在升溫成本方面是不利的,因此,作為下限值,無特別限定,優(yōu)選為500℃以上。需要說明的是,即使不將裝入顆粒時的溫度控制在上述溫度的情況下,若在不產(chǎn)生燃燒、燒結(jié)的影響的短時間內(nèi)將顆粒裝入冶煉爐中,也沒有特別的問題。實施例下面,示出實施例和比較例,更具體地說明本發(fā)明,但是,本發(fā)明并不限定于以下實施例。[實施例1]將作為原料礦石的鎳氧化礦、鐵礦石、作為助熔劑成分的硅砂和石灰石、粘合劑混合,得到混合物。需要說明的是,不混合作為原料的碳質(zhì)還原劑。然后,在得到的原料粉末混合物中添加適量水分,用手捏成球狀的塊狀物。接著,為了使得到的塊狀物的固體成分為70重量%左右,水分為30重量%左右,對塊狀物吹300℃~400℃的熱風,實施干燥處理。制造不包含碳質(zhì)還原劑的球狀顆粒(尺寸(直徑):17mm)。另外,在下述表3中示出干燥處理后顆粒的固體成分組成。[表3]然后,在冶煉爐中,將作為碳質(zhì)還原劑的煤炭粉(碳含量:55重量%,粒度:0.4mm)在爐床上鋪滿,在鋪蓋于上述爐床上的碳質(zhì)還原劑上載置并裝入制造的100個顆粒,用作為碳質(zhì)還原劑的煤炭粉進一步覆蓋載置的顆粒。此時,用煤炭粉覆蓋顆粒以使從被覆蓋顆粒的上端至碳質(zhì)還原劑層的表面為止的厚度(圖3中的X)為約1mm(顆粒的大小(直徑)的約5%)。需要說明的是,將顆粒裝入冶煉爐時,在600℃以下的溫度條件下進行。接著,將還原溫度設定為1400℃,在冶煉爐內(nèi)進行還原加熱處理。觀察還原加熱處理開始三分鐘后(在顆粒表層形成金屬殼后,金屬殼不溶解,維持顆粒形狀的時間范圍)的狀態(tài),數(shù)出崩解顆粒的個數(shù),作為顆粒崩解的比例,基于上述個數(shù)計算崩解個數(shù)/裝入個數(shù)的百分率(%)。其結(jié)果,在實施例1中,崩解的顆粒的比例為0%,完全沒有崩解的顆粒。然后,繼續(xù)進行還原加熱處理的結(jié)果是,顆粒不崩解且維持其形狀,同時,冶煉反應有效地進行,得到金屬與爐渣接合的“不倒翁”狀的塊狀物。[比較例1]在顆粒的制造中,混合作為原料的碳質(zhì)還原劑,制造顆粒,在僅將上述顆粒載置在鋪蓋在爐床上的碳質(zhì)還原劑的狀態(tài)下進行還原加熱處理。另外,在冶煉爐內(nèi),沒有用碳質(zhì)還原劑覆蓋顆粒。除此之外的條件與實施例1相同。其結(jié)果,在比較例1中,崩解顆粒的比例為15%,而且不能抑制顆粒的崩解。然后,繼續(xù)進行還原加熱處理的結(jié)果是,對于崩解的顆粒而言,由于顆粒崩解,因此,不能得到金屬與爐渣接合的“不倒翁”狀的塊狀物。[比較例2]在顆粒的制造中,不混合作為原料的碳質(zhì)還原劑,而制造不含有碳質(zhì)還原劑的顆粒,在僅將上述顆粒載置在鋪蓋在爐床上的碳質(zhì)還原劑上的狀態(tài)下進行還原加熱處理。另外,在冶煉爐內(nèi),沒有用碳質(zhì)還原劑覆蓋顆粒。除此之外的條件與實施例1相同。其結(jié)果,在比較例2中,崩解顆粒的比例為0%,完全沒有崩解的顆粒。但是,接著,進行還原處理的結(jié)果是,由于顆粒表面處于未與碳質(zhì)還原劑接觸的狀態(tài),因此,冶煉反應不能有效地進行,不能得到金屬與爐渣接合的“不倒翁”狀的塊狀物。當前第1頁1 2 3