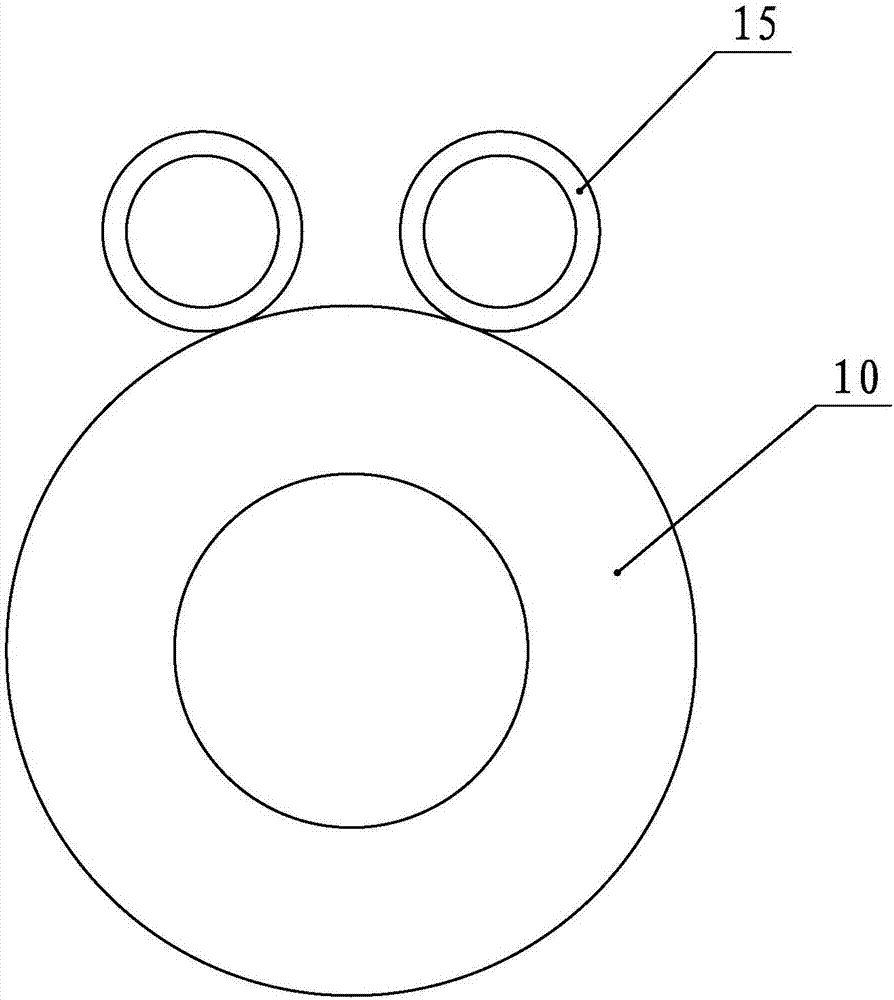
本發(fā)明涉及一種擠壓絲錐螺紋磨床,特別涉及一種擠壓絲錐螺紋磨床的組合式多線磨輪。
背景技術:
:擠壓絲錐是利用金屬塑性變形原理而加工內螺紋的一種新型螺紋刀具,擠壓絲錐擠壓內螺紋是無屑加工工藝,特別適用于強度較低、塑性較好的銅合金和鋁合金,也可用于不銹鋼和低碳鋼等硬度低、塑性大的材料攻絲,壽命長。用擠壓絲錐擠出的螺紋表面光潔度高,螺紋的金屬纖維不斷裂,并在表面形成一層冷硬層,可提高螺紋的強度和耐磨性,從根本上解決了攻絲的排屑困難問題,因無屑而更有利于螺紋的裝配,在電子、塑料行業(yè)應用廣泛。目前常規(guī)的擠壓絲錐為三棱或四棱結構,三棱邊的絲錐在擠壓螺孔時塑性變形和扭矩值最小,但其橫截面積小,因而其強度較四棱邊結構的強度差,且測量是用比較儀測量而存在測量誤差;而四棱邊擠壓絲錐塑性變形和扭矩值較三棱邊的擠壓絲錐稍大,但其測量是用三針在指示千分尺上測量,與比較儀測量方式比較其測量值相對準確。常規(guī)的擠壓絲錐加工采用金剛石磨輪進行單線磨,由于擠壓絲錐多為三棱或四棱結構,采用常規(guī)的單線磨具有效率低且加工精度差的缺點,因而多線磨是目前用于擠壓絲錐加工的新興方式。目前,多線磨金剛石磨輪只能采用表面層鍍覆結構,該種表面鍍覆結構的多線磨金剛石磨輪如果用于加工尖峰r<0.1mm的小螺距型面時則只能使用180#以上的金剛砂進行鍍覆,但表面鍍覆的金剛砂壽命與粒度成正比,則金剛砂的粒度越小壽命越差,從而導致現(xiàn)有技術的鍍覆結構金剛石磨輪用于小螺距型面加工時壽命較差且成本較高。而目前只有單片的金剛石磨輪才能用金剛砂實體燒結并用天然金剛石磨輪磨削精加工而成,但目前的單片金剛石磨輪不能滿足三棱或四棱結構擠壓絲錐的高效高精度加工且不能用于0.35mm以下小螺距擠壓絲錐的加工成型。技術實現(xiàn)要素:為解決上述技術問題,本發(fā)明提供了一種擠壓絲錐螺紋磨床的組合式多線磨輪,包括磨輪本體及位于所述磨輪本體一側的一對螺距錯位的金剛石修正輪;所述磨輪本體包括:多片并列組合的金剛石輪片,穿過組合的所述金剛石輪片中心定位孔的定位基體,與所述定位基體配合以夾持組合的所述金剛石輪片兩側的夾板,以及用于將所述定位基體、組合的所述金剛石輪片以及夾板進行組裝固定的螺釘;所述金剛石輪片的外邊緣螺紋尖角的截面呈60°夾角。其中,多片并列組合的所述金剛石輪片的直徑依次減小且最大直徑與最小直徑之差為△h。進一步的,單片的所述金剛石輪片均包括具有中心定位孔的輪片本體,以及環(huán)狀設置于所述輪片本體外徑的金剛石基體,多片并列組合的所述金剛石輪片的輪片本體直徑相等,且多片并列組合的所述金剛石輪片的金剛石基體的直徑依次減小且最大直徑與最小直徑之差為△h,其中,所述金剛石基體的外圓與內圓直徑之差為h,所述金剛石輪片的外徑為d,所述輪片本體的外徑為d0=d-2h。其中,所述輪片本體的厚度為b,所述金剛石基體的厚度為b,所述金剛石基體的厚度b小于所述輪片本體的厚度b。其中,按所述金剛石輪片的直徑由小到大排列,直徑倒數(shù)最小的三片所述金剛石輪片之間的兩個螺距t2相等,其余n片所述金剛石輪片之間的螺距t1相等。其中,所述金剛石輪片的螺距為0.7~2mm,所述金剛石輪片的數(shù)量為6-17片,且螺距越小對應的數(shù)量越多。通過上述技術方案,本發(fā)明具有如下優(yōu)點:①采用多片單獨精加工而成的金剛石輪片組合形成多線磨輪,相比于現(xiàn)有的單線磨,本發(fā)明多線磨輪可以使工件一次性加工吃刀到位,并一次性磨全程而使工效提高數(shù)倍;②采用多片單獨精加工而成的金剛石輪片組合形成多線磨輪,相比于現(xiàn)有的表面鍍覆金剛砂的多線磨輪,本發(fā)明多線磨輪具有更長的使用壽命而極大降低了加工成本;③采用主磨輪與一對螺距錯位的金剛石修正輪組合結構,通過金剛石修正輪的修正可以獲得螺距在0.35~0.7mm之間的小螺距擠壓絲錐的高效加工成型,解決了目前單純的厚度小于0.7mm多線磨輪難以成型的難題;④采用多片金剛石磨輪外徑階梯式結構,可以有效實現(xiàn)精度公差的分配而提高擠壓絲錐螺紋的加工精度。附圖說明為了更清楚地說明本發(fā)明實施例中的技術方案,下面將對實施例描述中所需要使用的附圖作簡單地介紹。圖1為本發(fā)明實施例所公開的組合式多線磨輪結構示意圖;圖2為本發(fā)明實施例所公開的磨輪本體截面結構示意圖;圖3為本發(fā)明實施例所公開的金剛石輪片截面示意圖;圖4為圖3中k處放大結構示意圖。圖中數(shù)字表示:10.磨輪本體11.定位基體12.夾板13.螺釘14.金剛石輪片15.金剛石修正輪16.輪片本體17.金剛石基體具體實施方式下面將結合本發(fā)明實施例中的附圖,對本發(fā)明實施例中的技術方案進行清楚、完整地描述。參考圖1,本發(fā)明提供的擠壓絲錐螺紋磨床的組合式多線磨輪,包括磨輪本體10及位于磨輪本體10一側的一對螺距錯位的金剛石修正輪15。參考圖2,磨輪本體10包括:多片并列組合的金剛石輪片14,穿過組合的金剛石輪片14中心定位孔18的定位基體11,與定位基體11配合以夾持組合的金剛石輪片14兩側的夾板12,以及用于將定位基體11、組合的金剛石輪片14以及夾板12進行組裝固定的螺釘13;金剛石輪片14的外邊緣螺紋尖角的截面呈60°夾角;多片并列組合的金剛石輪片14的直徑依次減小且最大直徑與最小直徑之差為△h。參考圖3及4,單片的金剛石輪片14均包括具有中心定位孔18的輪片本體16,以及環(huán)狀設置于輪片本體16外徑的金剛石基體17,多片并列組合的金剛石輪片14的輪片本體16直徑相等,且多片并列組合的金剛石輪片14的金剛石基體17的直徑依次減小且最大直徑與最小直徑之差為△h,其中,金剛石基體17的外圓與內圓直徑之差為h,金剛石輪片14的外徑為d,輪片本體16的外徑為d0=d-2h;其中,輪片本體16的厚度為b,金剛石基體17的厚度為b,金剛石基體17的厚度b小于輪片本體16的厚度b;按金剛石輪片14的直徑由小到大排列,直徑倒數(shù)最小的三片金剛石輪片14之間的兩個螺距t2相等,其余n片金剛石輪片14之間的螺距t1相等。其中,t與d及△h的對應關系具體參考表1:其中,t與b、b及d的對應關系具體參考表2:當擠壓絲錐的螺距≤0.7mm時,采用一對螺距錯位的金剛石修正輪15進行修正可獲得0.35~0.7mm螺距的擠壓絲錐。其中,金剛石輪片14的螺距為0.7-2mm,金剛石輪片14的數(shù)量為6-17片,且螺距越小對應的數(shù)量越多,具體參考表:3:基本螺紋螺距t(mm)金剛石輪片14數(shù)量(片)0.7170.75160.8151121.25101.581.75726本發(fā)明采用多片單獨精加工而成的金剛石輪片14組合形成多線磨輪,相比于現(xiàn)有的單線磨,本發(fā)明多線磨輪可以使工件一次性加工吃刀到位,并一次性磨全程而使工效提高數(shù)倍;采用多片單獨精加工而成的金剛石輪片14組合形成多線磨輪,相比于現(xiàn)有的表面鍍覆金剛砂的多線磨輪,本發(fā)明多線磨輪具有更長的使用壽命而極大降低了加工成本;采用主磨輪與一對螺距錯位的金剛石修正輪15組合結構,通過金剛石修正輪15的修正可以獲得螺距在0.35-0.7mm之間的小螺距擠壓絲錐的高效加工成型,解決了目前單純的厚度小于0.7mm多線磨輪難以成型的難題;采用多片金剛石磨輪外徑階梯式結構,可以有效實現(xiàn)精度公差的分配而提高擠壓絲錐螺紋的加工精度。對上述實施例的多種修改對本領域的專業(yè)技術人員來說將是顯而易見的,本文中所定義-般原理可以在不脫離本發(fā)明的精神或范圍的情況下,在其它實施例中實現(xiàn)。因此,本發(fā)明將不會被限制于本文所示的這些實施例,而是要符合與本文所公開的原理和新穎特點相一致的最寬的范圍。當前第1頁12