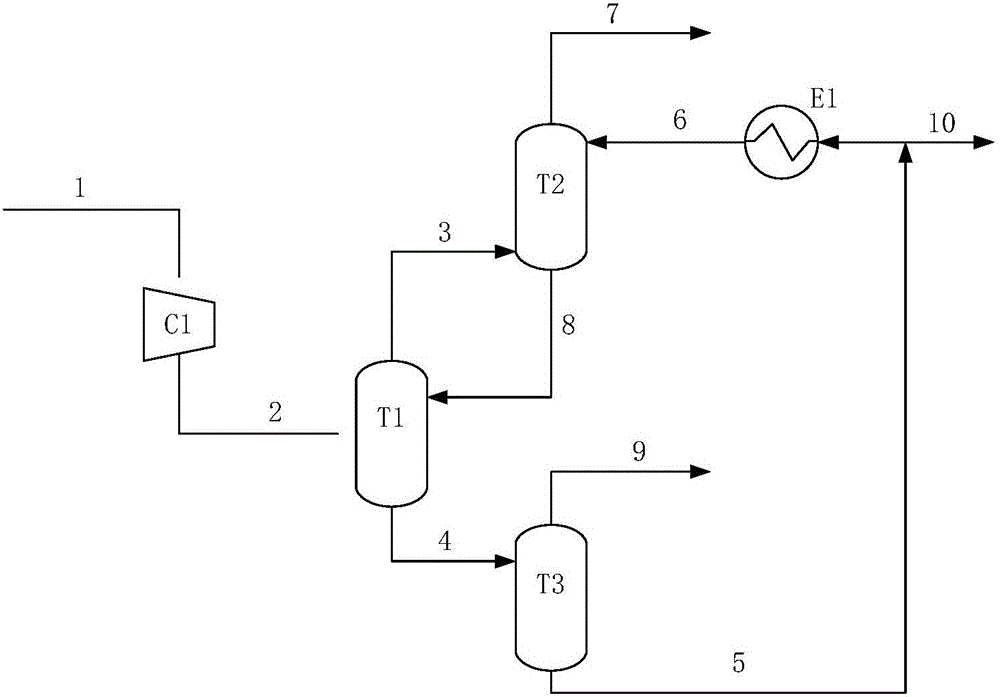
本發(fā)明涉及一種醇和/或醚制烯烴產(chǎn)物分離和副產(chǎn)利用的方法。技術(shù)背景乙烯、丙烯是一種需求量很大的基本有機(jī)化工原料,受環(huán)氧乙烷、聚乙烯、聚丙烯、丙烯腈、異丙苯、環(huán)氧丙烷等乙烯、丙烯衍生物需求的增長,相應(yīng)乙烯、丙烯的需求也快速增長。傳統(tǒng)的乙烯和丙烯主要來自于石油加工過程,隨著石油資源的日益匾乏,發(fā)展由煤或天然氣等非石油資源制備乙烯、丙烯的技術(shù)越來越引起國內(nèi)外的重視。由煤制乙烯、丙烯通常采用煤制合成氣、合成氣制取甲醇、再經(jīng)醇和/或醚制乙烯、丙烯的工藝路線。其中煤制合成氣和合成氣制取甲醇工藝技術(shù)已經(jīng)非常成熟。醇和/或醚制乙烯、丙烯技術(shù)經(jīng)過多年發(fā)展,也已經(jīng)實(shí)現(xiàn)了工業(yè)化,其代表的技術(shù)有中國石化的S-MTO技術(shù)、大連物化所D-MTO技術(shù)、UOP的MTO技術(shù)、Lurgi的MTP技術(shù)、中國石化的S-MTP技術(shù)等。但是由于醇和/或醚制乙烯、丙烯產(chǎn)物組成復(fù)雜,產(chǎn)物包括碳一至碳九甚至更重的組分,普遍存在分離工藝流程長、裝置能耗高的問題。如何降低醇和/或醚制乙烯、丙烯工藝的能耗,尤其是開發(fā)低能耗的產(chǎn)物分離方法,成為需要重點(diǎn)研究的課題。傳統(tǒng)烴類產(chǎn)物分離普遍采用精餾分離。典型的分離流程包括前脫甲烷的順序分離流程、前脫乙烷分離流程和前脫丙烷分離流程。例如在CN1431982A專利中,醇和/或醚制丙烯反應(yīng)產(chǎn)物經(jīng)過冷卻分離出烴類和水后,氣相烴類經(jīng)前脫乙烷流程首先分離出碳二及更輕組分和碳三及更重組分,然后在脫丙烷塔中分離出含有丙烯的碳三組分和碳四及更重組分,由于碳二烯烴和碳四碳五烯烴都可以在醇和/或醚制丙烯反應(yīng)器中進(jìn)一步轉(zhuǎn)化為丙烯,從脫乙烷塔獲得的碳二及更輕組分和從脫丙烷塔獲得的碳四及更重組分部分的返回醇和/或醚制丙烯反應(yīng)器。傳統(tǒng)的烴類產(chǎn)物分離方法由于采用了精餾操作,要么是高壓來提高精餾塔的操作溫度,要么是采用低溫冷劑,因此普遍存在能耗高的問題。美國專利US5326929提出了一種用溶劑吸收分離氫、甲烷與碳二組分的方法。但是該方法在大于3.2MPa的壓力下再生溶劑,導(dǎo)致再生溫度很高,高達(dá)150℃,溶劑再生后又 需要降溫冷卻,從而導(dǎo)致該工藝能耗巨大。中國專利CN101353286提出了一種含輕質(zhì)氣體的非深冷低碳烴分離方法。該方法首先把進(jìn)料氣體通過壓縮機(jī)升壓至2.0至4.0MPa,然后通過預(yù)切割塔分離把大部分碳二組分和甲烷分離,然后在吸收塔中用溶劑吸收甲烷中夾帶的碳二。由于大部分碳二和全部的碳三及更重組分在預(yù)分離塔中切出,吸收塔的氣相進(jìn)料負(fù)荷下降,吸收劑用量也相應(yīng)的下降,因此,該專利稱該方法的能耗比現(xiàn)有油吸收分離技術(shù)的能耗低。但是當(dāng)進(jìn)料氣體中含有碳六及更重組分時(shí),該方法由于沒有把碳六及更重組分從吸收劑中切出,導(dǎo)致大量的碳六及更重組分在吸收解吸系統(tǒng)中循環(huán),使得能耗會大幅增加,吸收效率下降,吸收解析系統(tǒng)中的塔設(shè)備塔徑增大,從而也使得投資也相應(yīng)增加。而在醇和/或醚制烯烴工藝中,反應(yīng)產(chǎn)物中含有一定量的碳六及更重組分,因此采用該方法不可避免的會有能耗高、投資增加的缺點(diǎn)。由于現(xiàn)有技術(shù)均存在裝置能耗高、、副產(chǎn)利用的問題,本發(fā)明有針對性的解決了上述問題,充分利用副產(chǎn)。技術(shù)實(shí)現(xiàn)要素:本發(fā)明所要解決的技術(shù)問題是現(xiàn)有技術(shù)中存在裝置能耗高、副產(chǎn)利用的問題,提供一種醇和/或醚制烯烴產(chǎn)物分離和副產(chǎn)利用的方法。該方法用于醇和/或醚制烯烴產(chǎn)物的分離時(shí)具有能耗低、經(jīng)濟(jì)性好、副產(chǎn)利用充分的優(yōu)點(diǎn)。為解決上述問題,本發(fā)明采用的技術(shù)方案如下:一種醇和/或醚制烯烴產(chǎn)物分離和副產(chǎn)利用的方法,包含如下步驟:醇和/或醚在反應(yīng)器中轉(zhuǎn)化為烯烴為主要反應(yīng)產(chǎn)物,反應(yīng)產(chǎn)物經(jīng)產(chǎn)品氣濃縮區(qū)濃縮后獲得混合烴類產(chǎn)物;混合烴類產(chǎn)物送入預(yù)分離塔中分離為碳五及更重組分和碳四及更輕組分;碳四及更輕組分經(jīng)增壓后送入吸收解吸系統(tǒng),分離為吸收尾氣、碳三組分、碳四組分;吸收尾氣作為乙苯反應(yīng)區(qū)的一股進(jìn)料;碳四組分至少部分返回醇和/或醚制烯烴反應(yīng)器。上述技術(shù)方案中,所述預(yù)分離塔操作壓力為0.1~1.2MPa,塔釜溫度為70~171℃。上述技術(shù)方案中,所述碳四及更輕組分增壓后壓力為1.0~2.0MPa。上述技術(shù)方案中,所述吸收解吸系統(tǒng)包含吸收塔、解吸塔和脫丙烷塔。上述技術(shù)方案中,所述脫丙烷塔釜獲得碳四組分,該碳四組分至少部分作為吸收塔的吸收劑。上述技術(shù)方案中,所述吸收尾氣與外界送入含苯物料在乙苯反應(yīng)區(qū)反應(yīng)生成乙苯。上述技術(shù)方案中,所述吸收塔操作壓力為1.0~1.6MPa,操作溫度為30~60℃,吸收劑用量為吸收塔氣相進(jìn)料質(zhì)量流量的1.0~3.0倍。上述技術(shù)方案中,所述解吸塔操作壓力為1.0~2.0MPa,塔釜操作溫度為60~100℃。上述技術(shù)方案中,所述脫丙烷塔操作壓力為0.6~1.5MPa,塔釜操作溫度為70~110℃。上述技術(shù)方案中,所述混合烴類產(chǎn)物中以重量百分比計(jì),碳五及更重組分的含量為大于2.2%。上述技術(shù)方案中,所述混合烴類產(chǎn)物中以重量百分比計(jì),碳五及更重組分的含量為大于4.1%。上述技術(shù)方案中,所述醇和/或醚為甲醇和/或二甲醚;更優(yōu)選的醇和/或醚為甲醇。上述技術(shù)方案中,所述一種醇和/或醚制烯烴產(chǎn)物的分離方法,包含如下步驟甲醇在反應(yīng)器中轉(zhuǎn)化為丙烯為主要反應(yīng)產(chǎn)物,經(jīng)脫水、含氧化合物和二氧化碳后獲得混合烴類產(chǎn)物,混合烴類物在預(yù)分離塔中分離為低壓碳四及更輕組分和碳五及更重組分;碳四及更輕組分經(jīng)過增壓后送入解吸塔;在解吸塔中碳三組分從塔釜采出得到脫丙烷塔進(jìn)料,全部的乙烯從解吸塔塔頂采出得到吸收塔進(jìn)料;在吸收塔中,以來自脫丙烷塔釜的碳四組分作為吸收劑吸收進(jìn)料中的丙烯,吸收液返回解吸塔;吸收尾氣與外界送入含苯物料在乙苯反應(yīng)區(qū)反應(yīng)生成乙苯,較好的利用了副產(chǎn);脫丙烷塔將脫丙烷塔進(jìn)料分離為碳三組分和碳四組分;碳三組分可以進(jìn)一步在丙烯精餾塔中分離出聚合級丙烯產(chǎn)品和丙烷;部分的碳四組分經(jīng)吸收劑冷卻器冷卻后送入吸收塔作為吸收劑,至少部分碳四組分返回醇和/或醚制烯烴反應(yīng)器,其余部分作為外排碳四組分排出。上述技術(shù)方案中,所述預(yù)分離塔的操作壓力高于混合烴類產(chǎn)物的壓力時(shí),采用增壓設(shè)備對混合烴類產(chǎn)物增壓至高于該操作壓力后送入預(yù)分離塔中。本發(fā)明打破了本領(lǐng)域技術(shù)人員的固有思維,沒有采用本領(lǐng)域技術(shù)人員很容易想到的通過在吸收解吸系統(tǒng)內(nèi)脫除碳五及更重組分,而是采用在混合烴類產(chǎn)物進(jìn)入吸收解吸系統(tǒng)前直接從中脫除碳五及更重組分的方法,以此來避免碳六及更重組分累積,從而造成吸收效率下降,能耗會大幅增加的現(xiàn)象。采用本發(fā)明的方法,混合烴類產(chǎn)物在預(yù)分離塔中脫除了碳五及更重組分,避免了碳六及更重組分在吸收解吸系統(tǒng)中的累積和循環(huán),降低了解吸塔釜和脫丙烷塔釜的溫度,從而降低了過程能耗;另一方面由于少了碳六及更重組分的累積和循環(huán),使得吸收解吸系統(tǒng)塔徑也相應(yīng)減小,從而也節(jié)省了設(shè)備投資費(fèi)用。采用本發(fā)明的方法,吸收解吸系統(tǒng)在較低的壓力下進(jìn)行,進(jìn)一步降低了解吸塔釜和脫丙烷塔釜的溫度,進(jìn)一步降低了過程能耗。吸收塔采用較高的吸收溫度,操作溫度為30~60 ℃,進(jìn)一步降低了冷量的消耗。脫丙烷塔釜獲得碳四組分至少部分可以作為吸收劑。采用本發(fā)明的方法,丙烯的回收率為99.99%,且能耗低,取得了較好的技術(shù)效果。附圖說明圖1為本發(fā)明所述方法的流程示意圖。圖1中,1為混合烴類產(chǎn)物;2為低壓碳四及更輕組分;3為高壓碳四及更輕組分;4為吸收塔進(jìn)料;5為脫丙烷塔進(jìn)料;6為吸收劑;7為吸收尾氣;8為吸收液;9為碳三組分;10為碳四組分;11為吸收劑;12為外排碳四組分;13為碳五及更重組分;101為甲醇進(jìn)料;102為返回的碳四組分;103為甲醇制丙烯反應(yīng)產(chǎn)物;104為廢水;105為含苯的流股;106位含乙苯的流股;R1為醇和/或醚制烯烴反應(yīng)器;R2為乙苯反應(yīng)區(qū);S1為產(chǎn)品氣濃縮區(qū);T1為預(yù)分離塔;C1為增壓設(shè)備;T2為解吸塔;T3為吸收塔;T4為脫丙烷塔;E1為吸收劑冷卻器。圖1的工藝流程如下:醇和/或醚在反應(yīng)器R1中轉(zhuǎn)化為烯烴為主要反應(yīng)產(chǎn)物,經(jīng)產(chǎn)品氣濃縮區(qū)S1濃縮后獲得混合烴類產(chǎn)物1。混合烴類物流1在預(yù)分離塔T1中分離為低壓碳四及更輕組分2和碳五及更重組分12。低壓碳四及更輕組分2經(jīng)過增壓設(shè)備C1增壓后獲得高壓碳四及更輕組分3后送入解吸塔T2。在解吸塔T2中碳三及組分更重組分從塔釜采出得到脫丙烷塔進(jìn)料5,全部的乙烯從解吸塔T2塔頂采出得到吸收塔進(jìn)料4。在吸收塔T3中,以來自脫丙烷塔釜的碳四組分6作為吸收劑吸收進(jìn)料4中的丙烯,吸收液8返回解吸塔T2。吸收尾氣7和含苯流股101一起送入乙苯反應(yīng)區(qū)R2,反應(yīng)后得到含乙苯流股102。脫丙烷塔T4將進(jìn)料5中分離出碳三組分9和碳四組分10。部分的碳四組分10經(jīng)吸收劑冷卻器E1冷卻后送入吸收塔T2作為吸收劑11吸收丙烯,部分的碳四組分102返回至反應(yīng)器R1,其余部分作為外排碳四組分12排出。圖2為采用碳四以上組分作為吸收劑的流程示意圖。圖2中,1為混合烴類產(chǎn)物;2為解吸塔進(jìn)料;3為吸收塔進(jìn)料;4為脫丙烷塔進(jìn)料;5為碳四及更重組分;6為吸收劑;7為吸收尾氣;8為吸收液;9為碳三組分;10為外排碳四及更重組分;C1為增壓設(shè)備;T1為解吸塔;T2為吸收塔;T3為脫丙烷塔;E1為吸收劑冷卻器。圖2的工藝流程如下:醇和/或醚在反應(yīng)器中轉(zhuǎn)化為丙烯為主要反應(yīng)產(chǎn)物,經(jīng)脫水、含氧化合物和二氧化碳后獲得氣相混合烴類產(chǎn)物1。氣相烴類物流1經(jīng)增壓設(shè)備C1增壓后,送入解吸塔T1。在解吸塔T1塔釜采出脫丙烷塔進(jìn)料4,全部的乙烯從解吸塔T1塔 頂采出得到吸收塔進(jìn)料3。在吸收塔T2中,以來自脫丙烷塔釜的部分碳四及更重組分5經(jīng)吸收劑冷卻器E1冷卻后作為吸收劑6送入吸收塔T2作為吸收劑吸收丙烯,吸收液8返回解吸塔T1。吸收尾氣7排出吸收解吸系統(tǒng)。脫丙烷塔T3進(jìn)料4在脫丙烷塔T3中分離為碳三組分9和碳四及更重組分5。下面通過實(shí)施例對本發(fā)明作進(jìn)一步的闡述,但不僅限于本實(shí)施例。具體實(shí)施方式【實(shí)施例1】采用本發(fā)明所述工藝方法,以30萬/年丙烯的甲醇或/和二甲醚制烯烴裝置為例,甲醇在醇和/或醚制烯烴反應(yīng)器R1中轉(zhuǎn)化為丙烯為主要反應(yīng)產(chǎn)物,經(jīng)產(chǎn)品氣濃縮區(qū)S1脫水和酸性氣體二氧化碳后獲得氣相烴類物流1。氣相烴類物流1溫度為43℃,壓力為0.10MPa。氣相烴類物流1在預(yù)分離塔T1中分離為低壓碳四及更輕組分2和碳五及更重組分12。低壓碳四及更輕組分2經(jīng)過壓縮機(jī)C1增壓至1.3MPa獲得高壓碳四及更輕組分3后送入解吸塔T2。在解吸塔中70%質(zhì)量分?jǐn)?shù)的碳三組分從塔釜采出得到脫丙烷塔進(jìn)料5,全部的乙烯從塔頂采出得到吸收塔進(jìn)料4。在吸收塔T3中,以來自脫丙烷塔釜的碳四組分6作為吸收劑吸收進(jìn)料4中的丙烯,吸收液8返回解吸塔T2。吸收尾氣7和含苯流股101一起送入乙苯反應(yīng)區(qū)R1,反應(yīng)后得到含乙苯流股102。脫丙烷塔T4將進(jìn)料5中分離出碳三組分9和碳四組分10。碳三組分9在后續(xù)的丙烯精餾塔中分離出聚合級丙烯產(chǎn)品和丙烷。50%質(zhì)量分?jǐn)?shù)的碳四組分103返還至反應(yīng)器R1增產(chǎn)烯烴,碳四組分部分經(jīng)吸收劑冷卻器E1冷卻至40℃后送入吸收塔作為吸收劑,其余部分作為外排碳四組分11排出。該工藝流程增產(chǎn)丙烯10.2%,丙烯回收率99.99%。各個(gè)塔的操作條件和系統(tǒng)能耗見表1。表中吸收塔吸收劑用量為吸收劑6的質(zhì)量流量和吸收塔進(jìn)料4的質(zhì)量流量之比。表中能耗為壓縮機(jī)、泵、換熱器、精餾塔能耗的總和。【實(shí)施例2】采用本發(fā)明所述工藝方法,以30萬/年丙烯的甲醇或/和二甲醚制烯烴裝置為例,甲醇在醇和/或醚制烯烴反應(yīng)器R1中轉(zhuǎn)化為丙烯為主要反應(yīng)產(chǎn)物,經(jīng)產(chǎn)品氣濃縮區(qū)S1脫水和酸性氣體二氧化碳后獲得氣相烴類物流1。氣相烴類物流1溫度為43℃,壓力為0.12MPa。氣相烴類物流1在預(yù)分離塔T1中分離為低壓碳四及更輕組分2和碳五及更重組分12。低壓碳四及更輕組分2經(jīng)過壓縮機(jī)C1增壓至1.6MPa獲得高壓碳四及更輕組分3后送入解吸 塔T2。在解吸塔中72%質(zhì)量分?jǐn)?shù)的碳三組分從塔釜采出得到脫丙烷塔進(jìn)料5,全部的乙烯從塔頂采出得到吸收塔進(jìn)料4。在吸收塔T3中,以來自脫丙烷塔釜的碳四組分6作為吸收劑吸收進(jìn)料4中的丙烯,吸收液8返回解吸塔T2。吸收尾氣7和含苯流股101一起送入乙苯反應(yīng)區(qū)R1,反應(yīng)后得到含乙苯流股102。脫丙烷塔T4將進(jìn)料5中分離出碳三組分9和碳四組分10。碳三組分9在后續(xù)的丙烯精餾塔中分離出聚合級丙烯產(chǎn)品和丙烷。60%質(zhì)量分?jǐn)?shù)的碳四組分102返還至反應(yīng)器R1增產(chǎn)烯烴,碳四組分部分經(jīng)吸收劑冷卻器E1冷卻至40℃后送入吸收塔作為吸收劑,其余部分作為外排碳四組分11排出。該工藝流程增產(chǎn)丙烯12.2%,丙烯回收率99.99%。各個(gè)塔的操作條件和系統(tǒng)能耗見表1。表中吸收塔吸收劑用量為吸收劑6的質(zhì)量流量和吸收塔進(jìn)料4的質(zhì)量流量之比。表中能耗為壓縮機(jī)、泵、換熱器、精餾塔能耗的總和?!緦?shí)施例3】采用本發(fā)明所述工藝方法,以30萬/年丙烯的甲醇或/和二甲醚制烯烴裝置為例,甲醇在醇和/或醚制烯烴反應(yīng)器R1中轉(zhuǎn)化為丙烯為主要反應(yīng)產(chǎn)物,經(jīng)產(chǎn)品氣濃縮區(qū)S1脫水和酸性氣體二氧化碳后獲得氣相烴類物流1。氣相烴類物流1溫度為43℃,壓力為0.14MPa。氣相烴類物流1在預(yù)分離塔T1中分離為低壓碳四及更輕組分2和碳五及更重組分12。低壓碳四及更輕組分2經(jīng)過壓縮機(jī)C1增壓至1.8MPa獲得高壓碳四及更輕組分3后送入解吸塔T2。在解吸塔中73%質(zhì)量分?jǐn)?shù)的碳三組分從塔釜采出得到脫丙烷塔進(jìn)料5,全部的乙烯從塔頂采出得到吸收塔進(jìn)料4。在吸收塔T3中,以來自脫丙烷塔釜的碳四組分6作為吸收劑吸收進(jìn)料4中的丙烯,吸收液8返回解吸塔T2。吸收尾氣7和含苯流股101一起送入乙苯反應(yīng)區(qū)R1,反應(yīng)后得到含乙苯流股102。脫丙烷塔T4將進(jìn)料5中分離出碳三組分9和碳四組分10。碳三組分9在后續(xù)的丙烯精餾塔中分離出聚合級丙烯產(chǎn)品和丙烷。70%質(zhì)量分?jǐn)?shù)的碳四組分102返還至反應(yīng)器R1增產(chǎn)烯烴,碳四組分部分經(jīng)吸收劑冷卻器E1冷卻至40℃后送入吸收塔作為吸收劑,其余部分作為外排碳四組分11排出。該工藝流程增產(chǎn)丙烯14.2%,丙烯回收率99.99%。各個(gè)塔的操作條件和系統(tǒng)能耗見表1。表中吸收塔吸收劑用量為吸收劑6的質(zhì)量流量和吸收塔進(jìn)料4的質(zhì)量流量之比。表中能耗為壓縮機(jī)、泵、換熱器、精餾塔能耗的總和?!緦?shí)施例4】采用本發(fā)明所述工藝方法,以30萬/年丙烯的甲醇或/和二甲醚制烯烴裝置為例,甲醇在醇和/或醚制烯烴反應(yīng)器R1中轉(zhuǎn)化為丙烯為主要反應(yīng)產(chǎn)物,經(jīng)產(chǎn)品氣濃縮區(qū)S1脫水和酸性氣體二氧化碳后獲得氣相烴類物流1。氣相烴類物流1溫度為43℃,壓力為0.16MPa。氣相烴類物流1在預(yù)分離塔T1中分離為低壓碳四及更輕組分2和碳五及更重組分12。低壓碳四及更輕組分2經(jīng)過壓縮機(jī)C1增壓至2.0MPa獲得高壓碳四及更輕組分3后送入解吸塔T2。在解吸塔中74%質(zhì)量分?jǐn)?shù)的碳三組分從塔釜采出得到脫丙烷塔進(jìn)料5,全部的乙烯從塔頂采出得到吸收塔進(jìn)料4。在吸收塔T3中,以來自脫丙烷塔釜的碳四組分6作為吸收劑吸收進(jìn)料4中的丙烯,吸收液8返回解吸塔T2。吸收尾氣7和含苯流股101一起送入乙苯反應(yīng)區(qū)R1,反應(yīng)后得到含乙苯流股102。脫丙烷塔T4將進(jìn)料5中分離出碳三組分9和碳四組分10。碳三組分9在后續(xù)的丙烯精餾塔中分離出聚合級丙烯產(chǎn)品和丙烷。70%質(zhì)量分?jǐn)?shù)的碳四組分102返還至反應(yīng)器R1增產(chǎn)烯烴,碳四組分部分經(jīng)吸收劑冷卻器E1冷卻至40℃后送入吸收塔作為吸收劑,其余部分作為外排碳四組分11排出。該工藝流程增產(chǎn)丙烯16.2%,丙烯回收率99.99%。各個(gè)塔的操作條件和系統(tǒng)能耗見表1。表中吸收塔吸收劑用量為吸收劑6的質(zhì)量流量和吸收塔進(jìn)料4的質(zhì)量流量之比。表中能耗為壓縮機(jī)、泵、換熱器、精餾塔能耗的總和。【比較例1】工藝流程見圖2,采用和實(shí)施例1相同的混合烴類產(chǎn)物,經(jīng)壓縮機(jī)增壓至1.6MPa后,送入解吸塔T1。解吸塔操作壓力1.5MPa,塔釜溫度96℃。在解吸塔T1中73.2%質(zhì)量分?jǐn)?shù)的碳三組分從塔釜采出得到脫丙烷塔進(jìn)料4,全部的乙烯從塔頂采出得到吸收塔進(jìn)料3。吸收塔操作壓力1.25MPa,吸收溫度43℃。在吸收塔T2中,以來自脫丙烷塔釜的碳四及更重組分5作為吸收劑吸收進(jìn)料3中的丙烯,吸收液8返回解吸塔T1。吸收尾氣7排出吸收解吸系統(tǒng)。脫丙烷塔進(jìn)料4在脫丙烷塔T3中分離為碳三組分9和碳四及更重組分5,脫丙烷塔操作壓力1.15MPa,塔釜溫度81℃,碳三組分9經(jīng)丙烯精餾獲得聚合級丙烯產(chǎn)品和丙烷。85%質(zhì)量分?jǐn)?shù)的碳四及更重組分5經(jīng)吸收劑冷卻器E1冷卻后送入吸收塔作為吸收劑6,其余部分排出系統(tǒng)。該工藝流程的丙烯回收率98.2%,能耗見表1?!颈容^例2】工藝流程見圖2,采用和實(shí)施例1相同的混合烴類產(chǎn)物,經(jīng)壓縮機(jī)增壓至1.4MPa后,送入解吸塔T1。解吸塔操作壓力1.3MPa,塔釜溫度74℃。在解吸塔T1中71.2%質(zhì)量分 數(shù)的碳三組分從塔釜采出得到脫丙烷塔進(jìn)料4,全部的乙烯從塔頂采出得到吸收塔進(jìn)料3。吸收塔操作壓力1.45MPa,吸收溫度44℃。在吸收塔T2中,以來自脫丙烷塔釜的碳四及更重組分5作為吸收劑吸收進(jìn)料3中的丙烯,吸收液8返回解吸塔T1。吸收尾氣7排出吸收解吸系統(tǒng)。脫丙烷塔進(jìn)料4在脫丙烷塔T3中分離為碳三組分9和碳四及更重組分5,脫丙烷塔操作壓力0.9MPa,塔釜溫度86℃,碳三組分9經(jīng)丙烯精餾獲得聚合級丙烯產(chǎn)品和丙烷。80%質(zhì)量分?jǐn)?shù)的碳四及更重組分5經(jīng)吸收劑冷卻器E1冷卻后送入吸收塔作為吸收劑6,其余部分排出系統(tǒng)。該工藝流程的丙烯回收率98.4%,能耗見表1。表1實(shí)施例1實(shí)施例2實(shí)施例3實(shí)施例4比較例1比較例2預(yù)分離塔操作壓力0.110.550.81.2--預(yù)分離塔頂操作溫度-13214156--預(yù)分離塔釜操作溫度72103144167--吸收塔吸收劑用量2.012.852.551.242.232.58吸收塔操作壓力1.051.251.351.551.251.45吸收塔釜操作溫度354347584344解吸塔操作壓力1.251.551.751.951.51.3解吸塔釜操作溫度637886959674脫丙烷塔操作壓力0.61.11.21.51.150.9脫丙烷塔頂操作溫度623.327472516脫丙烷塔釜操作溫度7392971098186能耗(kg標(biāo)油/kg丙烯)0.1720.1770.1830.1850.2260.231當(dāng)前第1頁1 2 3